Lista de verificación de inspección de recipientes a presión
Inspección externa
1. Grietas, sobrecalentamiento, deformación, fugas, etc. del cuerpo, superficie, uniones soldadas, etc. delrecipiente a presión; fugas de líquido y gas de los orificios de control del rendimiento del sello.
2. Corrosión de la superficie exterior, daño a la capa de aislamiento, descamación, humedad, pérdida de aire enfriado; vibración anormal, ruido y fricción de tuberías o componentes adyacentes.
3. Daños en los cojinetes y soportes, hundimiento de los cimientos, inclinación, agrietamiento y apriete de los pernos.
4. Compruebe si los accesorios de seguridad cumplen los requisitos especificados.
Inspección estructural
1. Conexión, junta de esquina, junta de solape y soldadura de la carcasa cilíndrica y la cubierta de la carcasa;
2. Bocas cuadradas, bocas de hombre, bocas de inspección y su refuerzo;
3. Cubierta, cojinete y soporte de la carcasa;
4. Brida y salida de desagüe.
Inspección de dimensiones geométricas
1. La cantidad de desalineación de las soldaduras longitudinales y circunferenciales, el ángulo de los bordes y esquinas, el refuerzo de la soldadura, el espesor de la soldadura de filete y el tamaño y disposición del ángulo de soldadura y la costura de soldadura.
2. Diámetro máximo y mínimo en la misma sección, superficie de la cubierta de la carcasa, altura del borde recto y arrugas longitudinales, placa gruesa desigual (forja), la situación de la junta.
3. La verticalidad del recipiente de presión vertical y el puntal del recipiente de presión esférico.
4. El espacio entre las tiras de acero adyacentes del recipiente a presión enrollado en cinta.
Inspección de defectos superficiales
1. Se debe medir y registrar la profundidad, el diámetro, la longitud y la distribución de la corrosión y el daño mecánico. Es necesario comprobar las razones de la corrosión anormal.
2. Se debe inspeccionar la soldadura en la superficie interior (incluida la zona cercana a la costura). En una de las siguientes situaciones, la inspección de la superficie se realizará en no menos del 20 % de la longitud de la soldadura: grado de resistencia del material superior a 540 MPa; fabricado en acero Cr-Mo; revestimiento de soldadura de acero inoxidable austenítico; el medio tiene tendencia a la corrosión bajo tensión; otras soldaduras sospechosas. Si se encuentra una grieta, el inspector determinará el porcentaje de detección de fallas en la superficie en función de los posibles defectos que puedan existir. Si aún existen grietas, se debe realizar una inspección de la superficie de todas las soldaduras.
Mientras tanto, es necesario inspeccionar más a fondo los defectos de grietas que puedan existir en la soldadura de la superficie exterior. Si la soldadura en la superficie interna tiene partes agrietadas, las soldaduras en sus respectivas superficies externas deben revisarse.
3. Preste especial atención a las piezas de concentración de tensión, las piezas deformadas, las piezas soldadas de acero diferentes, las huellas de soldadura de los dispositivos de trabajo, los daños por arco y las piezas que tienden a agrietarse.
4. Si existe una tendencia a la corrosión intergranular, se puede utilizar un examen metalográfico o una inspección por martilleo. Al martillar, use un martillo de mango de 0,5 a 1,0 kg, golpee en ambos lados de la soldadura u otras partes.
5. La inspección de grietas en la superficie se llevará a cabo en las juntas soldadas de inicio y final de la tira de acero del recipiente a presión tipo cinta.
6. También se deben revisar otros materiales que son sensibles a la soldadura en busca de posibles grietas de soldadura.
Medición de espesor de pared
1. La ubicación de los puntos de medición debe ser representativa y el número debe ser suficiente. Registro después de la medición. Para determinar la posición del punto, generalmente se deben seleccionar las siguientes partes:
1.1. La parte cuyo nivel de líquido a menudo fluctúa;
1.2. partes fáciles de corroer y erosionar;
1.3. Al fabricar, la parte donde se adelgaza el espesor de la pared y la parte donde se produce la deformación durante el uso;
1.4. Piezas sospechosas encontradas al inspeccionar defectos superficiales.
2. Al medir el espesor de la pared con un medidor de espesor ultrasónico, si hay un defecto de laminación en el metal base, se debe aumentar el número de puntos de medición o se debe usar un detector de fallas ultrasónico para averiguar la distribución de la capa intermedia y la inclinación. a la superficie del metal base. Al determinar el espesor de la pared de un recipiente a presión en un medio de hidrógeno, si se encuentra que el espesor de la pared aumenta, se debe considerar la posibilidad de corrosión por hidrógeno.
Material
1. En general, se debe determinar el tipo y grado del material de los principales componentes de presión. Para materiales no especificados, recipientes a presión de acero sin requisitos especiales, verifique de acuerdo con el límite de resistencia del material de acero Q235; para tanques, cisternas y recipientes a presión con requisitos especiales, se debe determinar el material. Para aquellos que han sido probados y claramente procesados, la inspección no debe repetirse.
2. Si el material del componente principal receptor de presión está deteriorado o no, según las condiciones específicas, se puede determinar mediante análisis químico, medición de dureza, análisis espectral o examen metalográfico.
Recipiente a presión con la capa de recubrimiento
1. La eliminación de la capa de aislamiento debe determinarse de acuerdo con las condiciones de trabajo y las condiciones ambientales externas. En uno de los siguientes casos, la capa de aislamiento no se puede quitar:
1.1. Toda la superficie de la soldadura ha sido probada y calificada durante la fabricación;
1.2. Inspección aleatoria de piezas representativas, no se encontraron defectos, como grietas;
1.3. Sin pérdida de aire enfriado;
1.4. El ambiente externo tiene medidas anticorrosivas confiables;
1.5. Tener una experiencia de uso similar;
1.6. El inspector cree que no es necesario.
2. En el caso de recipientes a presión revestidos de metal, si se descubre que el revestimiento tiene corrosión penetrante, grietas, protuberancias o abolladuras locales, fugas de medios por los orificios de inspección, la capa de revestimiento se debe quitar parcial o completamente para determinar la corrosión u otros defectos de el cuerpo.
3. Si se utiliza acero inoxidable austenítico para soldar el revestimiento y se encuentran grietas, descamación o daños en el revestimiento, o si la temperatura de la pared del cuerpo es anormal durante el funcionamiento, el revestimiento debe retirarse parcial o completamente para determinar la condición de corrosión o otros defectos del cuerpo.
4. Para las superficies interior y exterior con una capa de cobertura, primero se debe inspeccionar la superficie interior. Si se encuentran defectos graves, como grietas, la capa de recubrimiento debe retirarse parcial o completamente de la superficie exterior para su inspección.
Inspección de defectos ocultos en cordones de soldadura
1. La parte soldada que ha sido reparada dos o más veces o ha sido resoldada durante el uso.
2. Si se encuentra la grieta superficial de la soldadura, se debe realizar la inspección de defectos ocultos de la costura de soldadura.
3. La parte donde la cantidad de desalineación y el ángulo del borde exceden el estándar.
4. La parte de la soldadura que gotea durante el uso.
5. Requerimientos del usuario o partes que el inspector considere necesarias. Si no hay anormalidad, no necesita ser inspeccionado nuevamente.
6. El inspector determinará el método de inspección y el número de inspecciones aleatorias de acuerdo con las circunstancias específicas.
Inspecciones de accesorios de seguridad
Las inspecciones de los accesorios de seguridad se llevan a cabo de acuerdo con las especificaciones pertinentes.
Inspección de sujetadores
Los pernos de alta presión deben limpiarse uno por uno. Compruebe si hay daños y grietas y, si es necesario, someta a pruebas no destructivas a la superficie.
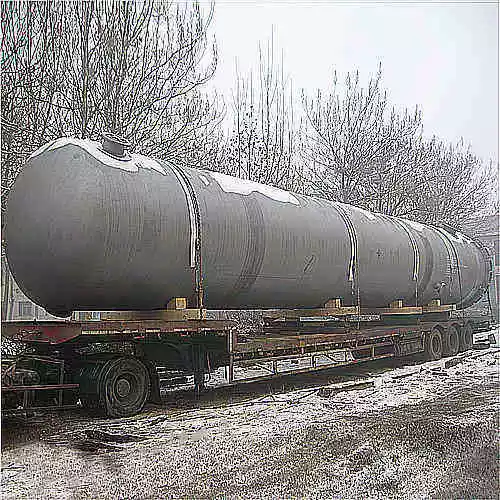