A guide of materials for cryogenic pressure vessels (part one)
The design of cryogenic pressure vessels is focused on material selection and, correspondingly, certain restrictions on manufacturing and construction. The steel used for the pressure components of the cryogenic pressure vessel must be killed steel. The allowable stress of the material is taken as the normal temperature, i.e. 20 °C, and the strength calculation method is in accordance with the GB 150.3 Standard.
At the end of the 19th century, a series of accidents related to low-temperature brittle fracture have occurred in rails, bridges and structural parts in the cold regions. Due to the limitations of science and technology at that time, the research on this kind of issue made no substantial progress. And in the 1940s, many ships, pressure vessels, pipelines, chemical equipment and large structures, especially some welded structures, had suffered from low-stress brittle fracture over and over, causing huge losses. Therefore, low temperature and low stress brittle fractures have become a topic of great concern in the industry. Through investigation and analysis of a large number of accidents, it can be concluded that low stress brittle fracture has the following characteristics:
1. When the fracture occurs, the working pressure of the pressure vessel is relatively low, the fracture nominal stress is lower than the yield strength of the material, and there is no or only local minimal plastic deformation before the fracture.
2. The speed rate of crack propagation is large.
3. Low-stress brittle fractures are mostly cleavage fractures or quasi-cleavage fractures, and the fractures have grain-like characteristics, which are bright and smooth.
4. Low-stress brittle fractures often occur on pressure vessels with notches or cracks, and various process defects and impurities present in the cylinder itself play a role as crack sources.
5. The fracture generally occurs at a low temperature, where the toughness of the material is poor.
Based on the characteristics of the above-mentioned low-stress brittle fracture combined with the fracture mechanics, it is found that the low-temperature toughness of the metal, that is, the micro-plastic deformation ability of the metal at the tip of the notch determines the ability of the pressure vessel to resist the brittle fracture.
Factors affecting low temperature toughness
1. Crystal structure
The results show that the ferritic steel with body-centered cubic matrix structure has higher brittle transition temperature and higher brittle fracture tendency, followed by hexagonal close-packed structure and face-centered cubic structure. Metals such as copper, aluminum, nickel and austenitic steels have essentially no such temperature effect, namely, no low stress brittle fracture.
In fact, unless there is a second phase or an environment that causes stress corrosion cracking, the face-centered cubic metal generally does not undergo brittle fracture. The main reason is that the yield strength of the face-centered cubic metal does not change significantly when the temperature is lowered, and it is not easy to produce deformation twins, the dislocations are easy to move, the local stress is easy to relax, the cracks are not easy to propagate, and there is generally no brittle transition temperature.
However, body-centered cubic metals are different. In the mid-temperature region, the strength (especially the yield strength) is significantly affected by impurities, load velocity and alloying elements. In regions where the temperature is below one fifth of the melting point of the metal, the yield strength increases rapidly with the decrease of temperature, and finally, it is almost equal to the tensile strength, and it is easy to cause deformation and twinning, thereby causing low stress brittle fracture.
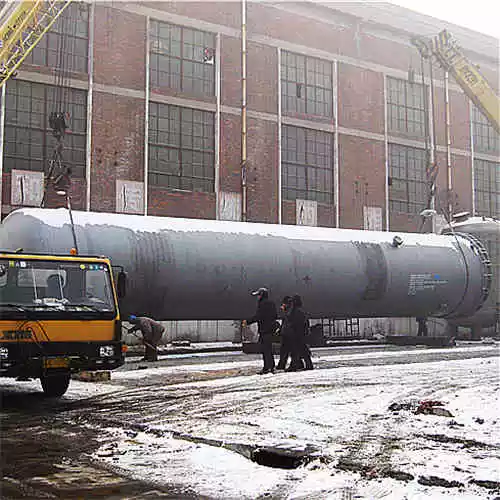