Air cooled heat exchanger corrosion prevention measure & rate test
Corrosion Rate Test
Corrosion rate is an important indicator for assessing the corrosion resistance of metals. When the metal is subjected to corrosion, its weight, structure, shape, surface state, mechanical properties, etc. will change. The macroscopic and microscopic rate of change can be used to reflect the degree of metal corrosion, so there will be different corrosion rate tests. Commonly used methods for air cooled heat exchanger tube bundles are electrical resistance method, weight loss method, linear polarization method, etc.
The electrical resistance method is based on the principle that when the cross-sectional area of metal is reduced due to corrosion, its electrical resistance increases. This method is fast, convenient, and can continuously monitor the corrosion condition of the equipment during the operation of air cooled heat exchanger tube bundle, accurately reflect the corrosion rate and its variation at each stage of operation, as well as be applicable to a variety of media.
Linear polarization method is very suitable for monitoring, which has characteristics of high sensitivity and fast response to changes in corrosion conditions. It can obtain instantaneous corrosion rate and reflect the changes of the working conditions of the tube bundles. But this method obtaining the corrosion rate is based on the steady state conditions, it cannot be used on partial corrosion since the object is measured as uniform or general corroded.
Weight loss method is simple, reliable, and commonly used for determining the corrosion rate. The test generally uses a hanging piece whose material is consistent with the pressure bearing material of the body of air cooled heat exchanger. The shape, size of the hanging piece can be based on the test condition and the need. Before the test, the piece should be surface-treated - be sanded, derusted and polished, then degrease the surface by solutions such as acetone. After that, rinse it with distilled water and dry it at 50℃. Immerse the hanging piece in an erosion solution, measure the corrosion rate by checking the weight of it.
Corrosion Prevention Measures
Reasonable selection of materials
Choosing the correct materials is one of the key process to control corrosion degree, and the following principles are: first, the corrosion resistance of the material should meet the requirements of the equipment environment, and the characteristics of the medium, such as the corrosion type and rate, sensitivity, etc; second, physical, mechanical properties and processing performance of materials should meet the design and processing requirements, including necessary strength, hardness, impact toughness, fatigue properties, heat resistance, weldability and so on. for air cooled heat exchanger tube bundles, under the conditions of media containing hydrogen and sulfur, it is better to choose nickel-based alloy, and duplex stainless steel, which is a new type of material with excellent corrosion resistance, high strength and easy manufacturing. The physical property of duplex stainless steel is between austenitic stainless steel and ferritic stainless steel, closer to ferritic stainless steel and carbon steel.
Reasonable Structural Design
The design of air cooled heat exchangers must proceed from anti-corrosion and be based on materials and environment with strict calculation, certain working stress and reasonable anti-corrosion structure design. It needs to pay attention to the following points: a simple shape, preventing water and dust accumulation, trying to avoid sharp corners, grooves and gaps, avoiding metal connections with large electric potential difference; avoiding working stress, assembly stress and residual stress in the same direction.
Manufacturing Process Improvement
During the processing and engineering, materials may be corroded or have potential of being corroded - Residual stress is easily generated during machining; the specifications of heat treatment should be carefully picked to avoid intergranular corrosion, stress corrosion, hydrogen embrittlement, etc. caused by improper heat treatment. And try to avoid heat preservation in the sensitized temperature zone. For heat treatment processes that may generate large residual stress, measures should be taken to eliminate residual stress; The corrosion sensitivity of materials is different according to different welding methods. In order to reduce the stress after welding, pay attention to the welding sequence so as to minimize the deformation of the workpiece. Residue should be cleaned in time to avoid local corrosion; For working piece welding, it should be degreased and cleaned immediately after welding and processing. Under certain working conditions, the internal air cooled heat exchanger tube bundle can adopt nickel-phosphorus plating method in order to prevent corrosion; The assembly stress should not be too excessive. To improve accuracy and reduce tolerance, a reasonable assembly method should be adopted to avoid stress concentration.
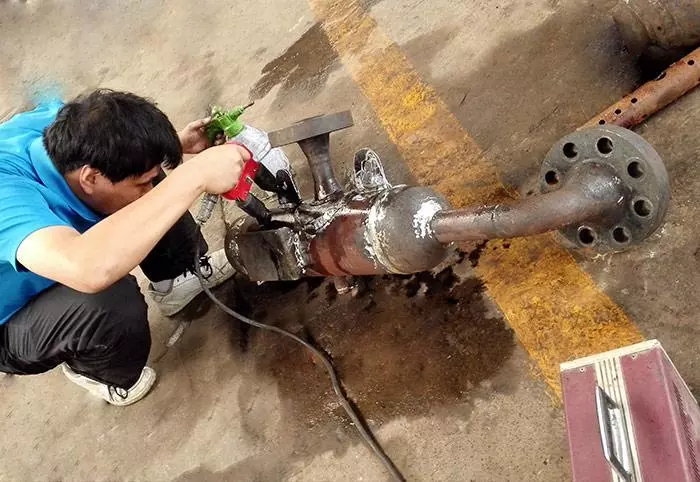