How to choose welding materials for pressure vessels (part one)
Pressure vessels have a wide range of applications, and their manufacturing processes are relatively complicated. It is necessary to strengthen the control of related processes to ensure that the quality meets the requirements of practical applications. Welding is the key in the manufacturing processes of pressure vessels, and it is a process that is prone to safety hazards. In the process of operation, it is important to select reasonable welding materials, ensure the accuracy of the process, solve the existing problems in time, and continuously optimize the welding technique, so as to ensure the safe and stable operation of pressure vessels, thereby improving the overall quality.
With the improvement of the manufacturing techniques and the changes in the social and economic situation, the size of the pressure vessel and the specific manufacturing requirements have been changed significantly, and the welding techniques have been adjusted and improved accordingly to meet the needs. Different positions of pressure vessels are required to be welded due to their large size. It is vital to strengthen the control of the welding process and select reasonable welding materials to ensure the quality of the pressure vessels and avoid security incidents.
There are many factors that will affect the welding process of a pressure vessel. Some high-strength and low-alloy steel materials have relatively high carbon and manganese content, which will have hardening effect after welding, giving rise to cracks in the steel structure. Although the cracks will not appear in a short time, but they will cause certain security risks. During the actual welding operation, the position of the welded joint is affected by the high temperature, and some elements will remain, which cannot be discharged after cooling, and will also lead to cracking of the welded joint. In addition, due to the high heat of the welding line, the large size of the crystal grains in the affected area, the lowering plasticity, softening may occur in some areas and cause the service life of the pressure vessel to decrease. Because the pressure vessel is bulky and the inner wall of the vessel is thick, during the actual operation, finding the weld seam and the microstructure is difficult. The traditional welding technique cannot meet the current production requirements, so it is necessary to combine the new techniques to achieve the welding accuracy, simplification, intelligentization, and axiomatization, which are also the main development directions of future welding techniques.
Main methods for selecting welding materials for pressure vessels
Welding materials need to be selected according to the specific performance of the product, including load performance, corrosivity, temperature, strength and other indicators. These factors can be clearly reflected in the design. The relevant data of the pressure vessel is mainly reflected in the design documents. It is necessary to read the data of the product in detail, clarify the design and use requirements, and reasonably select the welding materials. The selection of welding materials requires the specific implementation standards, important indexes such as high and low temperature performance, mechanical properties, and chemical composition, and calculating the carbon equivalent to provide data support for the later welding.
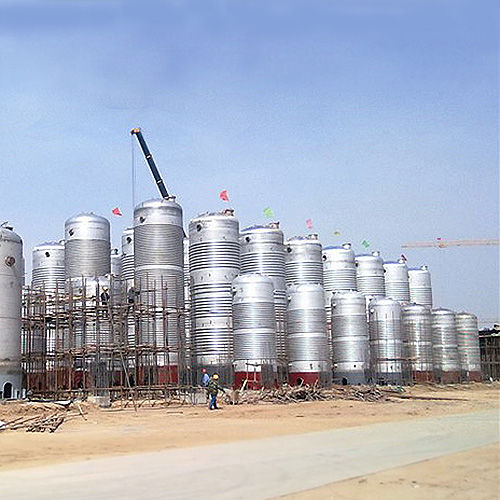