How to choose welding materials for pressure vessels (part two)
Low-temperature and low-alloy welding materials
When the equipment is operated below minus 20 °C, serious brittleness problems may occur. The metal structure and the composition of the alloy can be controlled to ensure the low-temperature operation performance of the equipment. The commonly used grades include 10MnDG, 09MnNiDR, 15MnNiDR and so on. When selecting a welding material, it is necessary to fully study its performance and grade at low temperatures to ensure its impact resistance. The lower the temperature the steel can be used under, the lower the strength under normal temperature conditions, and more complicated the replacement processes. First, the minimum temperature that the material to be welded can withstand should be clearly defined to determine the welding material. In the product design, the yield strength in the room temperature is 6 times of the stress, there is a certain thickness margin, and the material with good low temperature impact performance and low strength grade can be used for substitution.
Base and acid welding rods
Welding rods are widely used in various structures of welding, which have strong crack resistance, high impact toughness, and low diffusible hydrogen content of the deposited metal. But a welding rod needs to be strictly cleaned and dried before welding to avoid defects caused by oil, rust, and water. The welding operation has a certain difficulty and is highly demanded. In the actual welding process, acid welding rods with good process performance can be selected to ensure the welding effect. The pressure vessel has relatively high requirements on the strength, impact toughness and plasticity of the weld joint. Acid and base welding rods have no obvious difference when the same metal is welded. The impact toughness is different under the specific temperature. A base welding rod ensures that the deposited metal has sufficient impact absorption at minus 30 °C, while an acid welding rod ensures this function at 0 °C. Therefore, acid welding rods should be selected for products with operating temperatures above 0 °C to ensure that the overall quality of the boiler pressure vessel meets the requirements.
Austenitic stainless steel welding materials
Stainless steel is mainly used in situations with high temperature, low temperature or corrosion. It can be divided into duplex stainless steel, martensitic stainless steel, ferritic stainless steel, and austenitic stainless steel. Austenitic stainless steel is the most common one for pressure vessels. Due to the small strength difference among austenitic stainless steel materials, ultra-low carbon stainless steel welding materials are usually used in welding. Before selecting the welding materials, it is important to accurately grasp the actual operation of the product. For materials with high corrosion resistance and low temperature performance, austenitic stainless steel welding materials can be used, but this kind of material cannot be used under high temperature conditions.
Low-alloy high-strength steel and carbon steel welding materials
Low-alloy high-strength steel and carbon steel are mainly used in load-bearing structures without obvious oxidation and corrosion. The temperature range is between minus 20 °C and 425 °C. Materials with a higher strength class can be used without the need to re-evaluate the process. In the actual selection process, it is necessary to control the carbon equivalent and consider the need for stress corrosion. At the same time, it is essential to consider the influence of heat treatment. Pressure vessels generally adopt a heat treatment method that eliminates stress. After the temperature reaches a certain value, the overall strength of the weld joint will decrease. In addition, the strength of the weld is reduced after multiple thermal cycles.
Low alloy heat resistant steel welding materials
Low-alloy heat-resistant steel has good oxidation resistance and creep resistance performance under high temperature. Common grades include 15CrMo, 12Cr1MoV, 12CrMo, 15Mo, of which 12Cr1MoV has the widest application range. In the application process, technicians need to comply with relevant technical standards, master the allowable stress under different temperature conditions and the highest working temperature of different materials to ensure the rationality of the selection.
The welding quality of the pressure vessel directly determines its service life and safety. For this reason, technicians should strengthen the analysis of the actual situation, select reasonable welding materials, ensure the welding quality and safe production, avoid various accidents.
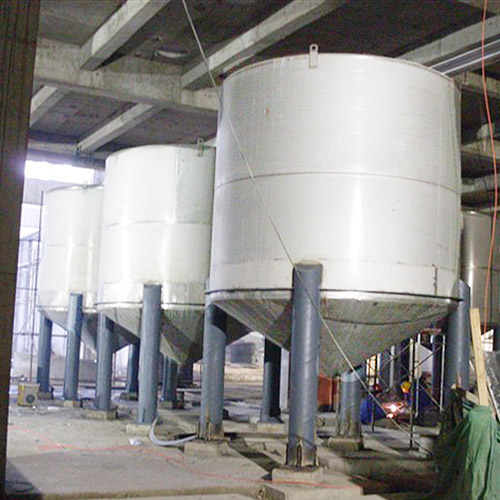