How to clean a plate heat exchanger
The main causes of scaling of plate heat exchanger and its perniciousness
During the use of plate heat exchangers, calcium, magnesium and carbonate in the water are decomposed into calcium carbonate and calcium hydroxide precipitates on the heating surface of the heat exchanger and form as hard scale. Due to the poor thermal conductivity of the scale, the heat exchanging efficiency of the device will reduce and the thermal energy will be seriously wasted.
Cleaning methods for plate heat exchanger scaling
Mechanical cleaning is the simplest cleaning method but it has disadvantages like scratching the plate and causing more scaling, poor working conditions for worker, large workload and damaging the plates and strips because the heat exchanger must be dismantled during cleaning.
Chemical cleaning (pickling) - It has been found through experiments that the choice of formic acid or oxalic acid as the cleaning solution is better than mechanical cleaning and does not corrode the plates of the heat exchanger.
Formic acid cleaning
The addition of a buffering agent and a surfactant to the formic acid solution provides a better cleaning effect and reduces the corrosion of the cleaning solution on the plates.
The basic principles of removing scale
1. The acid solution easily reacts with calcium, magnesium and carbonate containing in the scale and produce soluble compounds.
2. The acid solution dissolves the oxide on the metal surface and breaks the bond with the scale, so that the scale attached to the surface of the metal will be peeled off.
3. After the acid solution reacts with calcium, magnesium and carbonate, a large amount of CO2 will be generated, which has a certain force to peel off the scale that is difficult to dissolve or dissolve slowly from the heating surface.
4. For scale mixed with silicate and sulfate, since the oxides of calcium, magnesium, carbonate and iron are dissolved in the acid solution, the residual scale will become loose and easily washed away by the flowing acid solution.
Process requirements for cleaning scale
1. Temperature - Increasing the temperature for pickling is beneficial for improving the descaling effect. But the temperature should be kept around 60 ℃ because if the temperature is too high, it will aggravate the acid corrosion to the plates of the heat exchanger.
2. Concentration - For excellent cleaning effect, the pickling solution should be prepared following the apportionment which formic acid is 81.0%, water is 17.0%,buffer is 1.2% and surfactant is 0.8%.
3. Methods and time - The method of pickling should be under the combination of static soaking and dynamic cycling. Firstly, soak for two hours and then dynamically circulate for three hours - four hours. During the pickling process, the pickling concentration should be sampled frequently, and the pickling reaction can be considered as finished when the difference between the two adjacent assays is less than 1.2%.
4. Passivation treatment - After the pickling is finished, the scale and metal oxide on the surface of the plate heat exchanger are mostly dissolved and detached, the metal can be easily corroded. Therefore, the plates of the heat exchanger should be passivated.
Scale cleaning steps
1. Before pickling, firstly, flush the heat exchanger so that there are no impurities, such as mud and scale, inside the heat exchanger, which can improve the pickling effect and reduce the acid consumption.
2. The heat exchanger should be immersed in the acid solution for two hours, and then continuously circulated for three hours - four hours, during which the two sides should be alternately cleaned every 0.15 hours.
3. After the previous process is finished, if the pH of the acid solution is bigger than two, then the solution can be reused, otherwise, it should be diluted, neutralized and drained: After acid cleaning, use trisodium phosphate and softened water in a certain proportion to dynamically circulate the process of alkali washing in order to achieve acid-base neutralization. Then, repeatedly flush the heat exchanger with soften water for 0.15 hours.
Oxalic acid cleaning
Firstly, see if the oxalic acid can react with the scale and does not corrode the plates according to the materials of the plates and the color of the scale. In the test process, do not disassemble the heat exchanger, place a water injection valve on the inlet and outlet of the secondary network of the heat exchanger, inject 3% - 5% oxalic acid solution in the water tank into the heat exchanger, clean it by the circulation pump for 3-4 hours. Repeat the process one more time, and then disassemble the heat exchanger, if the plates are as clean as the new, the test can be considered as successful. Then wash the heat exchanger with 2% trisodium phosphate, flush it twice with water.
Washing the plates with oxalic acid must comply with the following requirements:
1. The water temperature must be less than 16℃;
2. The concentration of oxalic acid should be less than 5% and soaking time should not exceed six hours;
3. The water tank containing the solution should avoid light;
4. After pickling with oxalic acid, flush the heat exchanger with 2% trisodium phosphate and then water for two times;
5. The inlet and outlet of valve should be fastened, so that the solution won't flow into the system;
6. Put the cleaning solution into the water, not pump pit.
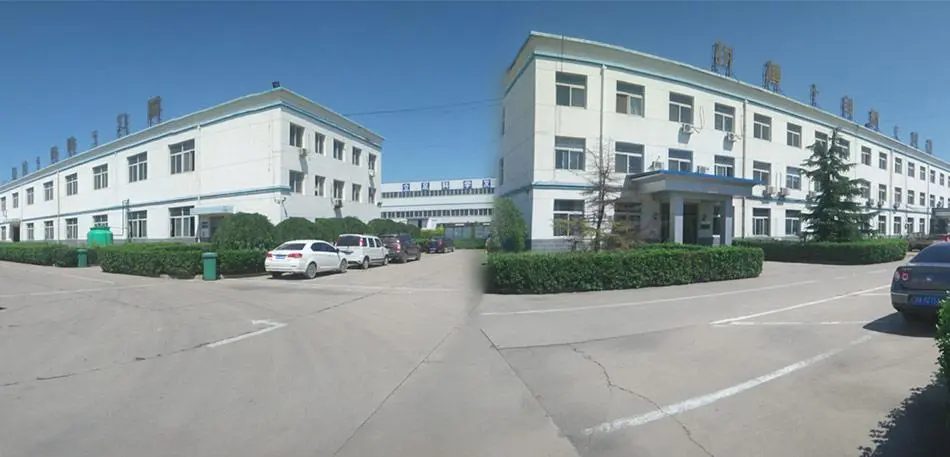