How to improve transfer efficiency of plate heat exchanger (part 1)
In recent years, plate heat exchangers have become more and more mature, with high heat transfer efficiency, small size, light weight, low-temperature resistance coefficient, convenient disassembly, various kinds, this type of heat exchangers has been widely used in the heating industry. According to assembly methods, plate heat exchangers can be classified into detachable, welded, brazed, plate-and-shell types, etc. Since detachable plate heat exchangers are easy to disassemble and clean, as well as of flexible area, they are one of the most used heat exchangers in heat supply engineering. Because they are limited by the heat resistance temperature of the rubber gasket, they are suitable for water-water heat transfer.
How to improve the efficiency of plate heat exchangers is a comprehensive economic benefit problem and should be determined through technical and economic comparisons. Improving the heat transfer efficiency of the heat exchanger and reducing its resistance should be considered at the same time, and the materials of the plate and the rubber gasket, as well as the installation method should be reasonably selected to ensure the safe operation of the equipment and prolong its service life.
The high-temperature and low-temperature fluids directly contact with and transfer heat through the plates. The key to improving the heat transfer efficiency of plate heat exchangers is to increase the heat transfer coefficient and the logarithmic mean temperature difference. Only by simultaneously increasing the surface heat transfer coefficient on both sides of the plate (with high thermal conductivity and thin) and reducing the thermal resistance of the fouling layer can the heat transfer coefficient of the heat exchanger be improved.
Increase the surface heat transfer coefficient of the plate
Since the corrugation of the plate heat exchanger enables the fluid to generate turbulence at a small flow rate (Reynolds number 150), a higher surface heat transfer coefficient, which is related to the geometry of the plate corrugations and the flow state of the medium, can be obtained. The waveforms of plates include herringbone shape, spherical shape and so on. After years of research and experiments, it is found that herringbone shape plate with triangular corrugated section has a relatively high surface heat transfer coefficient, and the larger the angle of the corrugation, the higher the flow velocity of the medium in the flow channel between plates, and the greater the surface heat transfer coefficient.
Reduce the thermal resistance of the fouling layer
The key to reducing the thermal resistance of the fouling layer of the heat exchanger is to prevent scaling. When the thickness of the scale is 1 mm, the heat transfer coefficient is reduced by about 10%. Therefore, it is necessary to pay attention to monitoring the water quality on both sides of the heat exchanger to prevent the impurities in the water from attaching to the plate.
Choose plates with high thermal conductivity
The materials of plates can be austenitic stainless steel, titanium alloy, copper alloy. The mostly-used material is stainless steel, which has good thermal conductivity, good stamping performance, lower price than titanium alloy, copper alloy, it is not easy to be oxidized, but easy to be corroded by chloride ion.
Reduce the thickness of the plate
The thickness of the plate is independent of its corrosion resistance but related to the pressure bearing capacity of the heat exchanger. When the thickness of the plate is increased, the pressure capacity of the heat exchanger is improved. For herringbone shape, the corrugations of the adjacent plates need to be in contact with each other to form a fulcrum with large density and uniform distribution. But the thickness of the plate has a great influence on the heat transfer coefficient - when the thickness is reduced by 0.1 mm, the total heat transfer coefficient of the symmetrical plate heat exchanger is increased by about 600 W/(m•K), and the asymmetric type is increased by about 500 W/(m•K). Under the premise of meeting the need of pressure bearing capacity, the thickness of the plate should be as small as possible.
Increase the logarithmic mean temperature difference
The flow patterns of plate heat exchangers include counterflow, parallel flow, and cross flow. Under the same working conditions, the logarithmic mean temperature difference in the counterflow is larger than that in the parallel flow while that in the cross flow is in between. The method of increasing the logarithmic mean temperature difference of the heat exchanger is to adopt counter flow or cross flow that is close to the counter flow. In addition, increase the temperature of the hot fluid and decrease the temperature of the cold fluid.
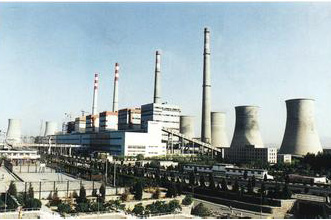