How to improve transfer efficiency of plate heat exchanger (part 2)
How to reduce the resistance of the heat exchanger
Increasing the average flow rate of the medium in the flow channel can increase the heat transfer coefficient and reduce the heat exchanger area. However, this will also increase the resistance of the heat exchanger, the power consumption of the circulating pump and the cost of the equipment. The power consumption of the circulation pump is proportional to the third power of the medium flow rate, so it is uneconomical to obtain a slightly higher heat transfer coefficient by increasing the flow rate. When the flow rate of the hot and cold medium is relatively large, the following methods can be used to reduce the resistance of the heat exchanger and ensure a high heat transfer coefficient.
Using hot mixing plates - The geometric structures on both sides of the hot mixing plate are the same. According to the angle of the herringbone shape corrugation, the plates can be divided into two kinds, one is with an angle bigger than 90-degree (normally around 120-degree), which has a high heat transfer coefficient, a large fluid resistance. The other is with an angle smaller than 90-degree (normally around 70-degree), which has a low heat transfer coefficient and small fluid resistance. The combination of these two kinds of plates can form three flow paths (HH, HL, LL) to meet the needs of different working conditions.
When the flow rate of the hot and cold media is relatively large, not like symmetrical single flow heat exchangers, heat exchangers with the hot mixing plates can reduce the area of the plate. The diameters of the angle holes on both sides of the hot and cold plates are generally equal. When the flow ratio of the hot and cold media is too large, the pressure at the angle on the side of the cold medium is greatly lost. In addition, the hot mixing plate design technique is difficult to achieve accurate matching, often resulting in limited plate area. Therefore, it is not advisable to use hot mixing plates when the flow ratio of the hot and cold media is too large.
The symmetrical plate heat exchanger is composed of plates with the same corrugated geometry on both sides. The cross-sectional areas of the hot and cold flow channels of this plate heat exchanger are the same. While asymmetrical (unequal cross-sectional area) plate heat exchangers change the waveform geometry of the two sides of the plate according to the heat transfer characteristics and pressure drop requirements of the hot and cold fluids, forming different flow cross-sectional areas. The angle on one side of the wide flow channel is larger. The heat transfer coefficient of the asymmetric plate heat exchanger will reduce slightly, and the pressure drop will greatly reduce. When the flow rate of the hot and cold media is relatively large, the asymmetric single flow can reduce the area of the plate by 15% to 30% compared with the heat exchanger with symmetric single flow.
When the flow rate of the hot and cold medium is large, a multi-flow combination arrangement may be adopted - The side with a small flow adopts more channels to increase the flow rate and obtain a higher heat transfer coefficient. The side with large flow uses fewer channels to reduce heat exchanger resistance. The average heat transfer temperature difference of mixed flow pattern is slightly lower. The fixed end and the movable end of the plate heat exchanger with multi-flow combination both connect with pipes, and the workload during maintenance is large.
Bypass pipes can be set at the inlet and outlet of the heat exchanger on the large flow side so as to reduce the flow rate and resistance if the flow rate of the hot and cold media is relatively large. For convenient adjustment, a regulating valve should be installed on the bypass pipe. This method should adopt a counter-current arrangement to make the temperature of the cold medium heat exchanger higher, and ensure that it can meet the design requirements after the flows are merged on the outlet. The heat exchanger bypass pipe can ensure the heat transfer coefficient and reduce the resistance, but the adjustment is slightly complicated.
The average flow velocity of the medium in the flow path between the heat exchanger plates is preferably 0.3-0.6 m/s, and the resistance is preferably not more than 100 kPa. According to the flow ratio of different cold and heat media, different types of plate heat exchangers can be selected. Bypass pipes can be used with symmetrical or asymmetrical, single-flow or multi-flow plate heat exchangers, but detailed thermal calculations should be performed.
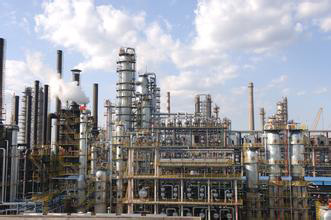