Pressure vessel inspection checklist
External inspection
1. Cracks, overheating, deformation, leakage, etc. of the body, surface, welded joints, etc. of the pressure vessel; liquid and gas leakage of seal performance checking holes.
2. Corrosion of the outer surface, damage to the insulation layer, peeling, moisture, cooled-air loss; abnormal vibration, noise, and friction of adjacent pipes or components.
3. Damage of the bearing and supporting, foundation sinking, tilting, cracking, and tightening of the bolts.
4. Check if the safety accessories meet the specified requirements.
Structural inspection
1. Connection, corner joint, lap joint and welding of the cylindrical shell and the shell cover;
2. Square holes, manholes, inspection holes and their reinforcement;
3. Shell cover, bearing, and supporting;
4. Flange and drainage outlet.
Geometric dimension inspection
1. The amount of misalignment of the longitudinal and circumferential welds, the angle of the edges and corners, the weld reinforcement, the thickness of the fillet weld and the size and arrangement of the weld angle, and weld seam.
2. Maximum and minimum diameter on the same section, shell cover surface, straight edge height and longitudinal wrinkles, unequal thick plate (forging), the situation of the joint.
3. The verticality of the vertical pressure vessel and the spherical pressure vessel strut.
4. The gap between the adjacent steel strips of the ribbon wound pressure vessel.
Surface defect inspection
1. The depth, diameter, length and distribution of corrosion and mechanical damage should be measured and recorded. The reasons of abnormal corrosion need to be checked.
2. The weld on the inner surface (including the near seam area) should be inspected. In one of the following situations, surface inspection shall be carried out not less than 20% of the length of the weld: material strength grade greater than 540MPa; made of Cr-Mo steel; austenitic stainless steel welding cladding; medium has stress corrosion tendency; other suspected welds. If a crack is found, the inspector shall determine the percentage of surface flaw detection based on potential defects that may exist.If cracks still exist, surface inspection of all welds should be performed.
Meanwhile, it is necessary to further inspect the crack defects that may exist in the weld of the outer surface. If the weld on the inner surface has cracked parts, the welds on their respective outer surfaces should be spot-checked.
3. Pay special attention to stress concentration parts, deformation parts, dissimilar steel welding parts, work fixture welding traces, arc damage and parts that tend to crack.
4. If there is a tendency to intergranular corrosion, metallographic examination or hammering inspection may be used. When hammering, use a handle hammer of 0.5 to 1.0 kg, knock on both sides of the weld or other parts.
5. Surface crack inspection shall be carried out on the steel strip start and end welded joints of the ribbon-type pressure vessel.
6. Other materials that are sensitive to welding should also be checked for possible weld cracks.
Wall thickness measurement
1. The location of the measurement points should be representative and the number should be sufficient. Record after the measurement. To determine the position of the point, the following parts should generally be selected:
1.1. The part whose liquid level often fluctuates;
1.2. easy to corrosion and erosion parts;
1.3. When manufacturing, the part where the wall thickness is thinned and the part where the deformation occurs during use;
1.4. Suspicious parts found when inspecting surface defects.
2. When measuring the wall thickness with an ultrasonic thickness gauge, if there is a lamination defect in the base metal, the measuring point number should be increased or an ultrasonic flaw detector should be used to find out the distribution of the interlayer and the inclination to the surface of the base metal. When determining the wall thickness of a pressure vessel in a hydrogen medium, if the wall thickness is found to increase, the possibility of hydrogen corrosion should be considered.
Material
1. The type and grade of the material of the main pressure components should generally be ascertained. For unspecified materials, steel pressure vessels without special requirements, check according to the strength limit of steel Q235 material; for tanks, tankers and pressure vessels with special requirements, the material must be ascertained. For those that have been tested and clearly processed, the inspection should not be repeated.
2. Whether the material of the main pressure-receiving component is deteriorated or not, according to the specific conditions, it can be determined by chemical analysis, hardness measurement, spectral analysis or metallographic examination.
Pressure vessel with the coating layer
1. Whether the insulation layer is removed should be determined according to the working conditions and external environmental conditions. In one of the following cases, the insulation layer may not be removed:
1.1. The entire surface of the weld has been tested and qualified when manufacturing;
1.2. Random inspection of representative parts, no defects, like cracks were found;
1.3. No cooled-air loss;
1.4. The external environment has reliable anti-corrosion measures;
1.5. Have a similar use experience;
1.6. The inspector believes that it is not necessary.
2. For metal-lined pressure vessels, if the lining is found to have penetrating corrosion, cracks, local bulges or dents, media leaking from the inspection holes, the lining layer should be removed partially or completely to ascertain the corrosion or other defects of the body.
3. If austenitic stainless steel is used to weld the lining, and cracking, peeling, lining damage are found, or if the wall temperature of the body is abnormal during operation, the lining shall be removed partially or completely to ascertain the corrosion condition or other defects of the body.
4. For the inner and outer surfaces with a covering layer, the inner surface should be inspected first. If serious defects such as cracks are found, the covering layer should be removed partially or completely on the outer surface for inspection.
Welding seam hidden defects inspection
1. The welded part that has been repaired two or more times or been re-welded during use.
2. If the surface crack of the weld is found, the welding seam hidden defects inspection should be performed.
3. The part where the amount of misalignment and the angle of the edge exceed the standard.
4. The part of the weld that leaks during use.
5. User requirements or parts deemed necessary by the inspector. If there is no abnormality, it needs not to be inspected again.
6. The method of inspection and the number of random inspections shall be determined by the inspector according to the specific circumstances.
Safety accessories inspections
Safety accessories inspections are carried out in accordance with the relevant specifications.
Fastener inspection
The high pressure bolts should be cleaned one by one. Check for damage and cracks and, if necessary, be surface nondestructive tested.
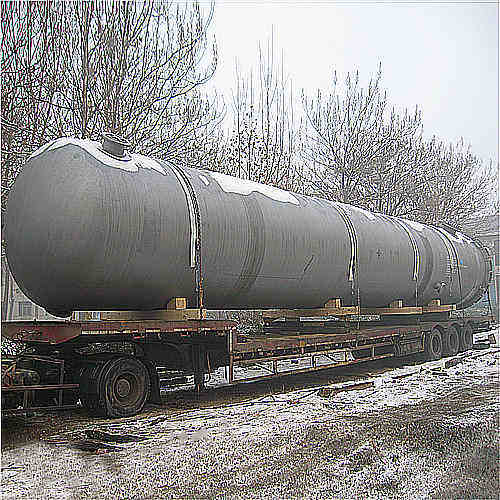