The corrosion causes of air cooled heat exchangers (part one)
As a large heat exchanging equipment, air cooled heat exchangers are widely used in the petrochemical industry. However, the tube bundles of air cooled heat exchanger are often used in high temperature, pressure and corrosion conditions, so the corrosion performance directly affect the safety and stable operation of equipment. This article will analyze the common types of corrosion of tube bundles and suggest protective measures to improve the service life of the product.
Pitting Corrosion
If the bearing materials contain dissolved oxygen and hazardous anions (like chloride ions), most of the surface of air cooled heat exchanger tube bundles will not corrode or just slightly corrode, but after a certain time, in some small areas, there will be cavity or pitting. And as time goes by, those tiny holes will continue to deepen.
The important influencing factors in the design and manufacturing of air cooled heat exchanger tube bundles include firstly, the effect of heat treatment aging temperature. For stainless steel tube bundles, the main bearing parts are generally not heat treated after welding. Except austenitic stainless steel has the best pitting resistance property after solution treatment. While for other stainless steel materials, heat treatment such as annealing or tempering at certain temperatures produces a precipitated phase, which increases the tendency of pitting corrosion. Secondly, as the surface finish of the metal tube bundles is improved, it will enhance the pitting resistance. But when the metal surface is hardened because of cold working, its pitting resistance will get weaker. Therefore, the pitting corrosion test is generally carried out for uncommonly used materials, which normally can be divided into three types: chemical immersion, electrochemical measurement, field test. The evaluation of pitting corrosion resistance includes pitting depth, density and speed rate, area, etc., and the pitting speed rate need to be combined with the distributing, shape, size, density, depth of the pore.
Crevice Corrosion
Crevice corrosion is caused by media for heat transfer stagnate in a small crevice between metals, or metal and non-metal (generally 0.025 mm-0.1 mm). This kind of media contains anions that will result in decrease in material strength and bearing capacity, an increase in local additional stress. In air cooled heat exchangers, crevice corrosion usually occurs in the lap joint of plates, the flange seal surface joint, the gasket seal, between the base pipe and liner tube, where crevice corrosion is most likely to generate, or between rust layers. Therefore, in the production design, the base pipe and the liner tube are often expanded during the whole process to eliminate the gap between the two. For air cooled heat exchangers, the wire plug sealing structure is usually adopted, being sealed by metal gasket, and both sides of the gasket are respectively contacted with the plug and tube sheet. From microcosmic view, there is a certain gap between the gasket and tube sheet that bears with heat transfer media. Due to factors such as pressure, temperature, vibration, etc., the crevice corrosion may generate on the sealing tip, which will easily lead to a failure of gasket sealing.
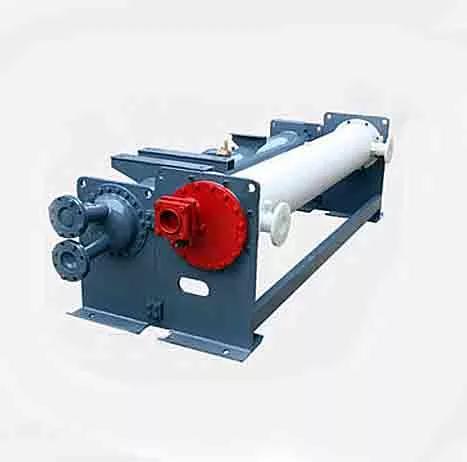