The inspection of pressure vessels
A pressure vessel is a sealed container for storing gases or fluids. Its operation pressure is much higher than the ambient pressure, so the vessels can be dangerous and may induct fatal accidents. Hence it is necessary to perform the inspection and safety testing of pressure vessels. We list some aspects about the inspection of pressure vessels as below.
External inspection
Also known as in-service inspection, the main contents of the inspection are: abnormalities on the outer surface of the pressure vessel, such as cracks, deformation, leakage, local overheating; whether the safety accessories are complete, sensitive and reliable; whether the fastening bolts are intact and all tightened; Whether the foundation has any abnormalities such as sinking, tilting, and damage to the coating. The external inspection is both the work of the inspector and the daily inspection of the operator. Any unsafe phenomenon (such as cracks, deformation, severe leakage, etc. of the pressure parts) should be reported to the relevant personnel in time and the valve system must be shut down.
Internal and external inspection
Internal and external inspection of the pressure vessel must be carried out after the parking and that the inside of the container have been cleaned. In addition to the entire contents of the external inspection, the main contents of the inspection also include examining the corrosion and wear of the inner and outer surfaces. Check if any cracks on welds, shell cover transition areas and other stress concentration parts with the naked eye and magnifier. If necessary, use ultrasonic waves or radiographic inspection to check the internal quality of the weld and measure the wall thickness. If the measured wall thickness is less than the minimum wall thickness of the container, the strength check should be re-examined, and the pressure-reducing use or repair measures should be proposed; for the container that may cause the metallographic structure change of the metal material, metallographic examination should be carried out if necessary; The main bolts of high and ultra-high pressure vessels should be checked with magnetic powder or coloring to find whether there are cracks on the pressure vessels or not. Through internal and external inspections, the defects should be analyzed and the treatment opinions submitted. A retest is required after repair. The internal and external inspection cycle of the pressure vessel is once every three years, but the inspection period of the container for strongly corrosive media and highly toxic media should be shortened. For containers with serious defects during operation and containers with poor welding quality and containers whose material with unknown resistance to corrosion, the inspection cycle should also be shortened.
Overall inspection
In addition to the above-mentioned inspection items, to conduct the overall inspection of a pressure vessel, a pressure-tight test (generally a hydrostatic test) is also required, including the nondestructive spot testing of major welds or inspection of all weld joints. However, for containers with low pressure, non-flammable or non-toxic, non-corrosive media, if no defects are found, after obtaining certain experience, nondestructive testing can be neglected. The overall inspection of the container is generally performed at least once every six years. For qualified containers filled with air and inert gas, the overall inspection cycle may be properly extended after obtaining experience and one or two internal and external inspections to confirm that there is no corrosion.
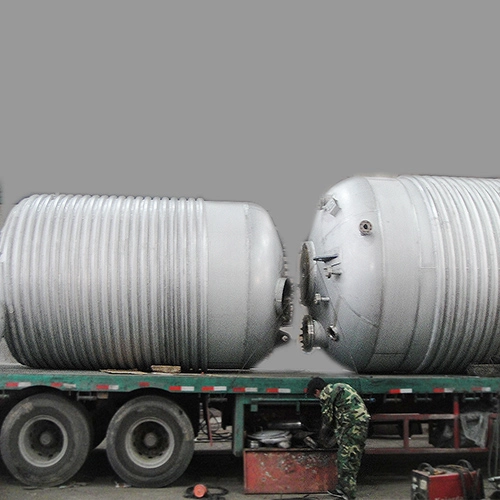